Wrentham Tool Group is EDM-capable, but what does that mean for you?
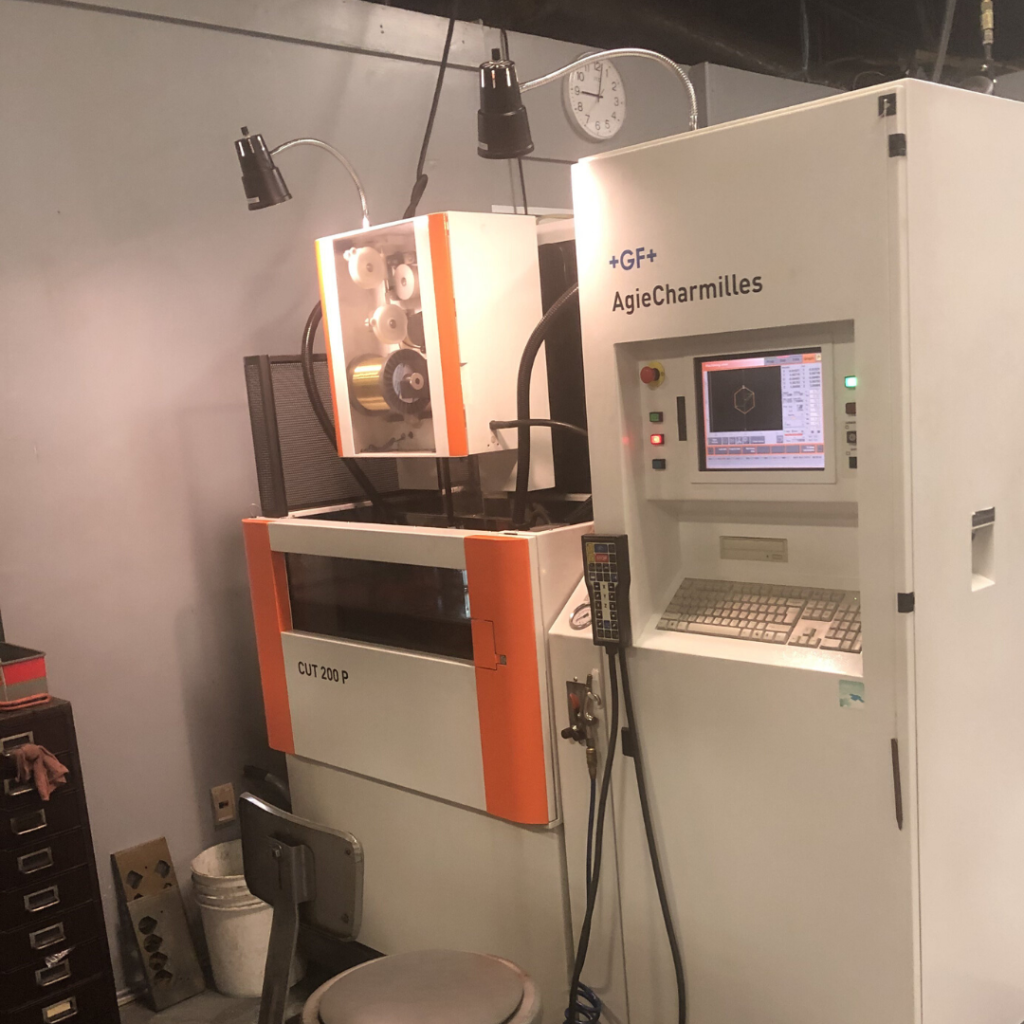
Wire EDM machines like this one use a wire to discharge their electric current.
What is EDM?
Electrical Discharge Machining (EDM) is an incredibly precise manufacturing technique in which material is removed from a workpiece using thermal energy. When applied to carbide and other hard materials, EDM is capable of creating extremely complex shapes that are difficult to achieve when milling while allowing material to be cut to extremely tight tolerances.
As explained by Encyclopedia Britannica:
EDM involves the direction of high-frequency electrical spark discharges from a graphite or soft metal tool, which serves as an electrode, to disintegrate electrically conductive materials such as hardened steel or carbide. The electrode and workpiece are immersed in a dielectric liquid, and a feed mechanism maintains a spark gap of from 0.0005 to 0.020 inch (0.013 to 0.5 millimeter) between the electrode and the workpiece. As spark discharges melt or vaporize small particles of the workpiece, the particles are flushed away, and the electrode advances. The process is accurate, but slow, and is used for machining dies, molds, holes, slots, and cavities of almost any desired shape.
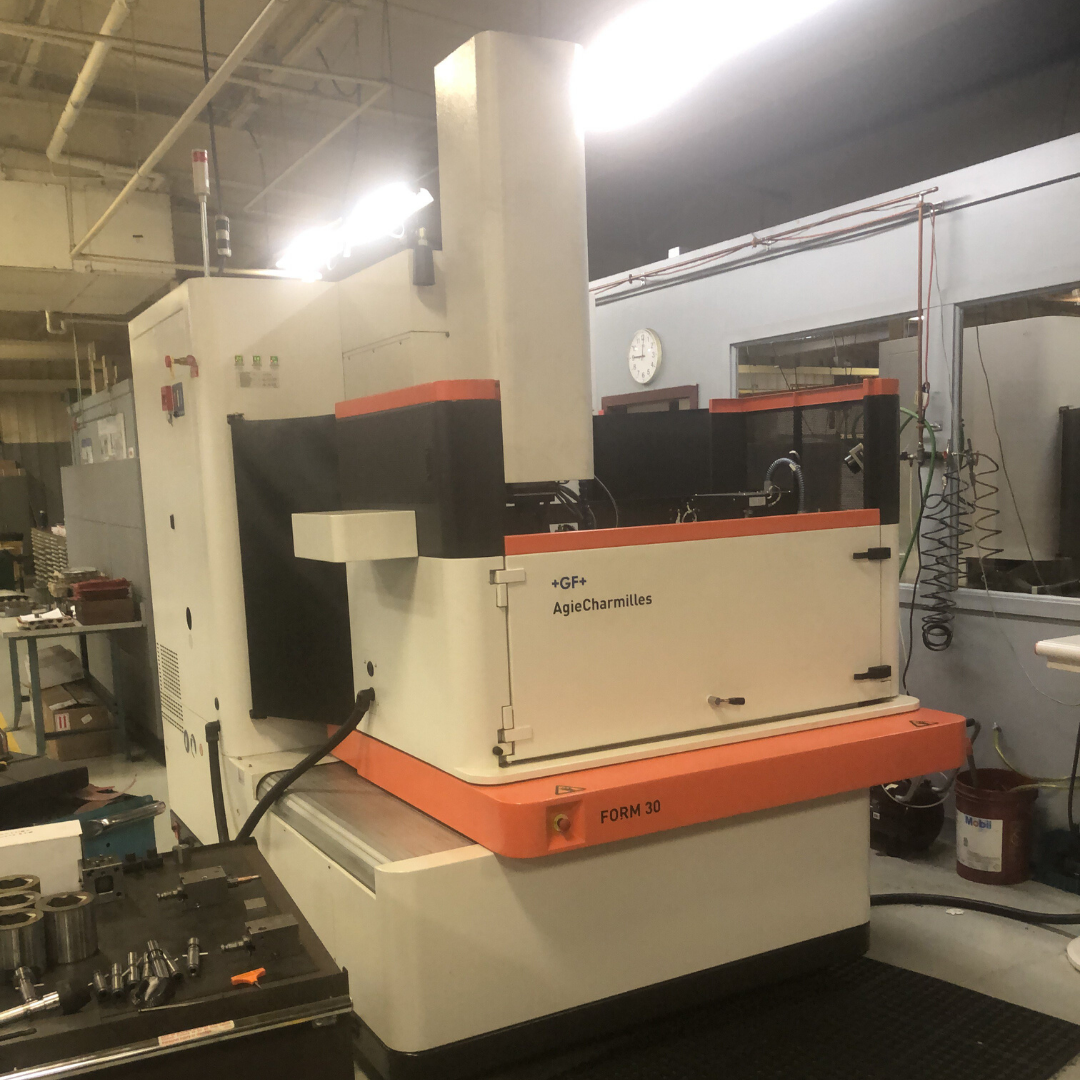
Meanwhile, Ram (or sinker) EDM machines use an electrode to discharge their current.
How does EDM improve what we can offer?
When we initially decided to improve upon our gaging offerings, it was clear that we needed to expand our capacity and quality in those areas. Investing in the latest state-of-the-art EDM technology has allowed us to manufacture a wider variety of gages with increased precision while also allowing us to expand our gage product offering.
Thanks to EDM technology, Wrentham Tool Group™ offers the following product families:
- Recess Gaging
- Nut Forming Dies
- Extrusion Dies
- Trim Dies
- Hex Recess Inserts
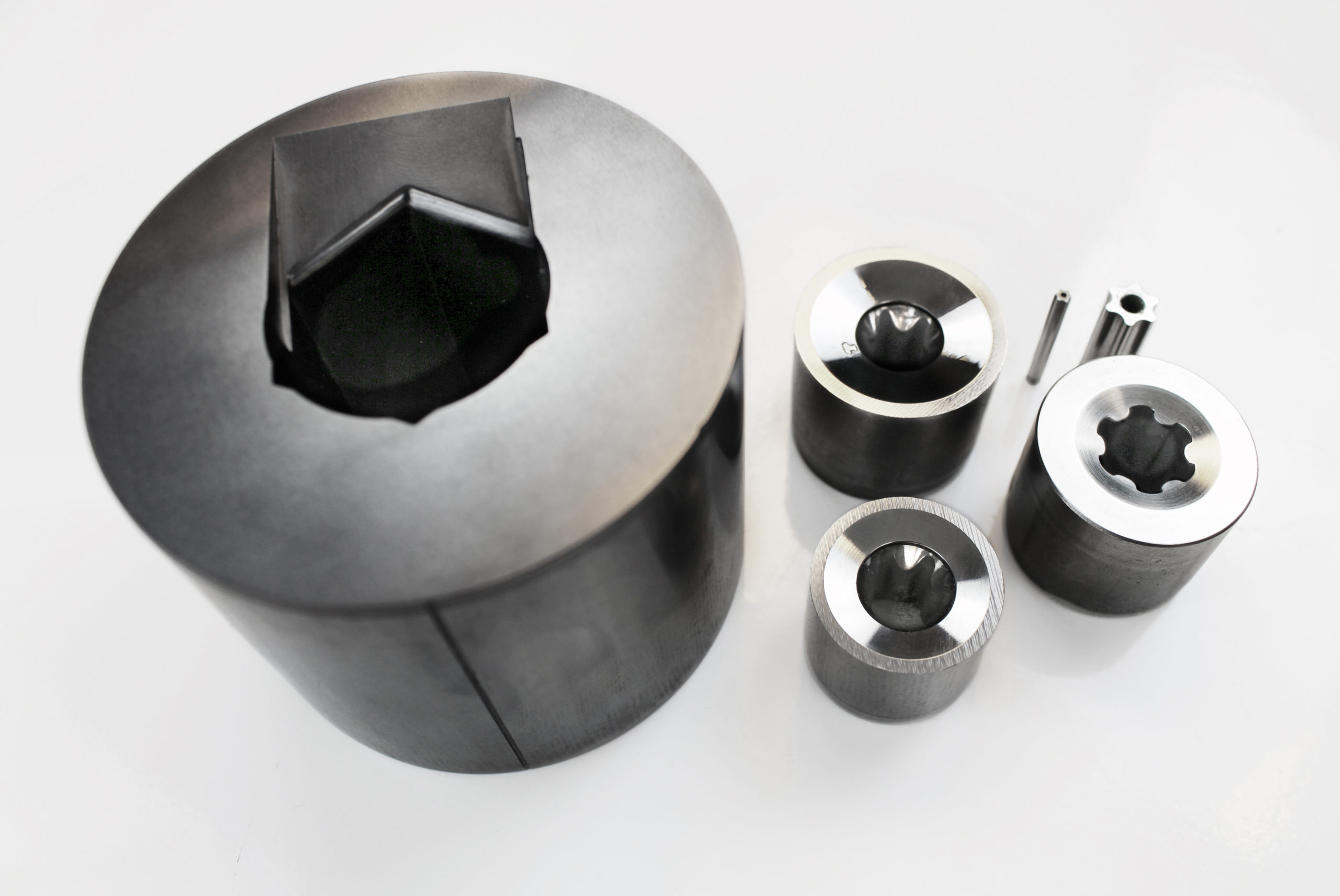
Pictured left to right: A nut forming die, 2 extrusion dies, a pin holder, and 2 Hexlobe® gage elements (size 50 & size 10). All of these products were manufactured using EDM technology

At Wrentham Tool Group™, we have the capacity to use both Wire and Ram (Sinker) EDM to create intricate and complex designs.
How is this valuable to our customers?
The accuracy and precision of the WIRE and RAM (sinker) EDM process allows us to manufacture to very tight tolerances. Depending on geometry and accounting for a small amount of measurement uncertainty, we can comfortably achieve a 0.0002” inch tolerance through EDM when working with materials with a surface finish of RA0.04 µm. Our accredited laboratory gives us the capability to measure to millionths of an inch. The ability to hold such tight tolerances provides our customers with consistent and repeatable tooling from one shipment to the next so that the customer can standardize their operation.
Another benefit of our EDM capability is that it allows us to support the header manufacturing process by producing very close tolerance cold forming and extrusion dies for our punch and pin production lines. In this process, accuracy is very important due to the inherent variation in manufacturing. This makes it very important to target a die size within the tolerance to accommodate that variation. EDM has allowed us to do so with more precision than ever before.
While EDM improves our header tooling, it also allows us the opportunity to provide general EDM service to customers.
According to Quality Assurance Manager Stephen Doldo, EDM technology allows Wrentham Tool Group™ to produce “virtually any straight or angled wall with any geometry that you can get a wire into.” This has allowed us to provide more customization and specialty items for our customers.